Authors: Gabriela Handley, Eric Owens- SPI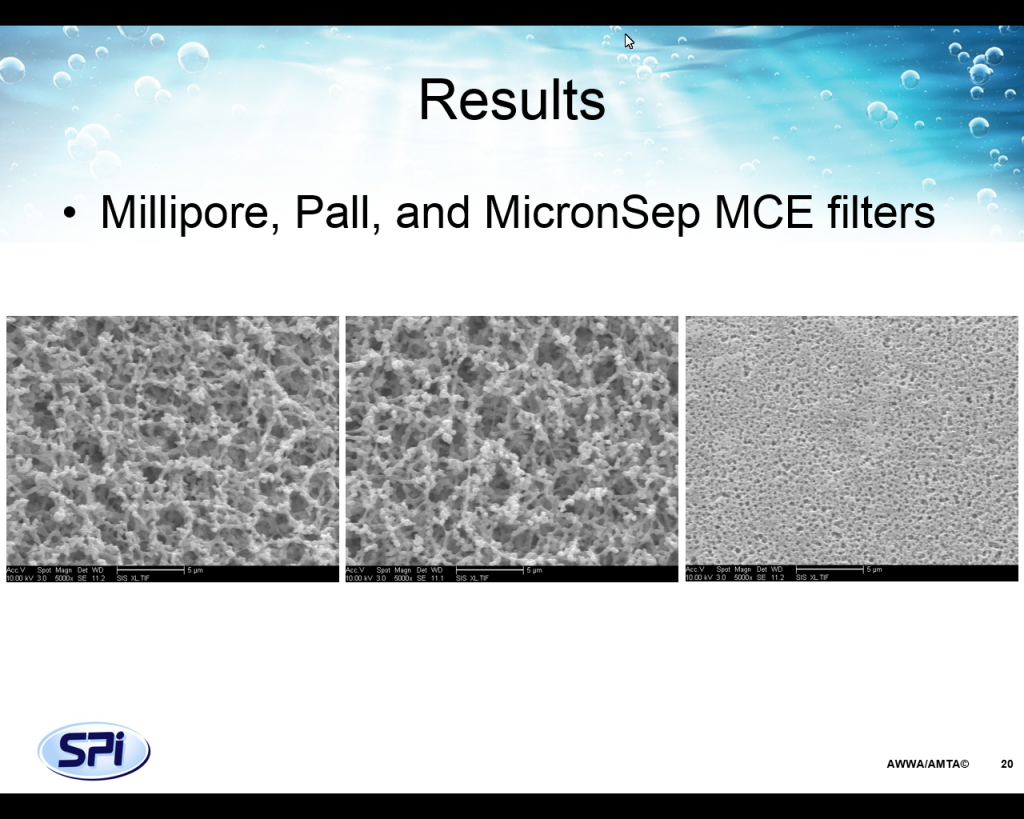
There is an ongoing debate about the benefit of the Silt Density Index (SDI) as an indicator of fouling potential for nanofiltration (NF) and reverse osmosis (RO) membrane. Some RO veterans will point to the fact that the cellulose acetate (CA) type filter pad originally used for performing SDI tests was intended to be representative of the fouling potential of cellulose acetate RO membrane, and not its successor, polyamide RO membrane. Others may point to experience that shows that the influence of other constituents in the water, such as organic material, will impact the SDI test and yield a result that is not reflective of particulate fouling on the membrane surface. But those that use this test routinely in real-world applications know that the most significant value the SDI test can provide is an indication of a change within their specific RO feed water source.
Regardless of whether the SDI test is considered valuable or not, the fact remains that most, if not all RO membrane manufacturer’s still require a maximum SDI limit within their standard terms and conditions for the membrane warranty. Whether or not an operator understands, appreciates, or even considers the SDI test result, in most cases they should be performing this test periodically to maintain compliance with their membrane warranty.
The SDI membrane filter pad is 47 mm in diameter with a 0.45 micron pore size. There are a variety of membrane chemistries available for membrane filters fitting these characteristics, including mixed cellulose esters (MCE, mixed cellulose acetate and cellulose nitrates), polyvinylidene fluoride (PVDF), Nylon, and polyethersulfone (PES). While there is some debate about which filter pad chemistry is appropriate for various applications, often times the membrane warranty language does not stipulate the material of the SDI filter pad required to maintain compliance with the warranty. Field experience at a variety of municipal facilities has demonstrated that very different SDI results are observed for different filter pad chemistries. Additionally, very different results can be obtained when using the “same” filter pad chemistries from different manufacturers.
This paper will document the SDI results generated from six different SDI filter pads on a variety of water types. The study considers the SDI results using filter pads of MCE, Nylon, PVDF, and PES chemistries. MCE filter pads from three different manufacturers were investigated, as this chemistry is arguably the most commonly used type for the SDI test. The feed waters for a variety of large-scale, municipal NF/RO facilities were used in the study, including three advanced water treatment plants, three brackish groundwaters, and three organic-laden potable water plants (groundwater and surface waters).
This paper will document the findings of this study and will demonstrate the need for consistency in the use and selection of SDI filter pad chemistries by membrane treatment plant operators for their specific facility. While it is not the authors’ intention to identify the “best” filter pad for use in the SDI test, the findings will illustrate the need for a thoughtful consideration of the filter pad used in the SDI test and how it may impact the operator’s ability to achieve the RO warranty conditions.